Центровка валов
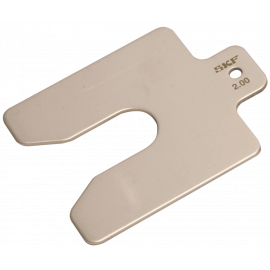
Что такое центровка валов и виды центровок валов
Центровка валов - это процесс выравнивания двух или более валов друг с другом в границах допустимого предела. Центровку считают произведённой, если отклонения валов от верной позиции положения размещены в границах стандартов, определённых сборочными чертежами или техническими условиями на изготовление агрегата.
Центровка бывает:
- горизонтальной;
- вертикальной.
При данных видах центровок подвижная деталь смещается до соответствия осей вращения в горизонтальной и вертикальной плоскости соответственно.
Центровка решает следующие проблемы:
- Вибрация. Из-за несоосности вращающиеся массы распределяются неоднородно, вследствие чего происходит вибрация.
- Потери мощности. Если нет центровки в месте соединения, образуются усилия трения, теряется полезная передаваемая мощность.
- Дополнительная нагрузка на опорные узлы — подшипники, сальники, шарнирные соединения, полумуфты. Игнорирование центровки уменьшает период работы узлов, повышает частоту и цену техобслуживания.
- Снижение эффективности. Из-за несоосности оборудование эксплуатируется менее расчётного режима. Потери от низкой производительности и простоя больше затрат на центровку.
- Ухудшение качества продукции. Из-за вибрации и функционирования во внештатных режимах технологический процесс нарушается, качество продукции ухудшается.
Подготовка к центровке валов
1.Подготовка рабочей зоны. Центровка вала начинается с уборки и обустройства рабочего места:
– от концов центрируемых валов удаляются лишние вещи (такелажная оснастка, инструмент, детали);
– убирают мусор с фундамента и около него;
– подводят переносное низковольтное освещение;
– укладывают в определённом месте все важные приспособления: канат для проворачивания валов краном, инструменты и приборы, цилиндровое масло для смазки подшипников, тетрадь, чтобы фиксировать итоги замеров, цветные карандаши (мел) для пометок на полумуфтах.
2. Проверка шеек валов. Шейки валов машин, прибывших в разобранном виде, хорошенько очищают от антикоррозионного покрытия чистыми тряпками, увлажнённые бензином, уайт-спиритом, ксилолом, деревянными скребками. Использовать иные скребки нельзя, дабы не испортить шлифованные покрытия. Поверхность обрабатывают чистой бязью или марлей, смоченной этиловым спиртом. Потом её промывают керосином и протирают насухо. Далее очищенную шейку вала осматривают. Если на шейках вала находятся царапины, риски или ржавчина, вал шлифуют следующим способом. На шейку вала располагают небольшое наждачное полотно, покрытое маслом, сверху – фетр или войлок. Концы наждачного полотна и фетра зажимают между фланцами полухомутов, чтобы для их вращения не понадобилось больших усилий. Вал шлифуют вращением отмеченного приспособления от руки.
Ниже представлено приспособление для шлифовки вала. Оно состоит из:
1 – полухомут;
2 – вал;
3 – фетр или войлок;
4 – наждачное полотно.
При шлифовке шеек вала наждачное полотно меняют спустя 15–20 минут, а позицию ротора изменяют каждый час поворотом его вокруг оси на 90°, 180°, 270° и так далее. Для полировки к наждачному полотну, смазанному маслом, включают мел. Полировать можно пастой ГОИ (названа благодаря аббревиатуре научного учреждения, где была разработана - Государственный оптический институт). Вместо наждачного полотна используют прессшпан или кожу, куда добавляют пасту ГОИ, разведённую керосином. После шлифовки и полировки шейки вала промывают керосином и вытирают насухо.
3. Проверка состояния полумуфт. Так же, как и шейки валов, полумуфты перед посадкой обрабатывают от антикоррозионного покрытия деревянными скребками, тряпками, пропитанным бензином, уайт-спиритом или ксилолом. Затем полумуфты промывают керосином, протирают насухо и осматривают. С появлением забоин, рисок или царапин аккуратно зачищают их наждачным полотном или шабером.
4. Подготовка полумуфт к насадке. Непосредственно от способа насадки замеряется посадочное отверстие ступицы полумуфты и диаметр конца вала. Важно удостовериться, что конусности в отверстии полумуфты и на посадочной части вала нет. Отверстие в ступице полумуфты и посадочная часть вала должны выполняться в виде цилиндра.
Измеряют микрометрическим нутромером (замер отверстия) и скобой с отсчётным устройством (замер диаметра вала) непременно в трёх местах: по длине ступицы, длине конца вала и в двух перпендикулярных плоскостях. Нутромер в отверстии ступицы полумуфт монтируют так, чтобы его ось была без наклона к оси отверстия, иначе измерения окажутся неверными. Итоги измерения отверстия нутромером проверяют с помощью прецизионного штангенциркуля.
У некоторых машин полумуфты насаживают с использованием фиксирующих деталей (шпонок, стопорных винтов и других) без подогрева или со слабым подогревом.
Взаимное положение валов
Взаимное положение валов влияет на надёжность и эксплуатационный ресурс оборудования. В момент центровки делают две операции:
- Выверку оси общего вала или выверку линии валов;
- Избавление от боковых и угловых смещений валов, то есть, непосредственно центровку.
Важно расположить валы соединяемых машин так, чтобы торцевые плоскости полумуфт в горизонтальной и вертикальной плоскостях располагались параллельно. Это нужно для нормального распределения нагрузок между подшипниками. Оси валов в данном случае должны являться продолжением друг друга без смещений. Испытывая давление собственного веса ротора, форма оси вала каждой машины становится немного изогнутой.
При строго горизонтальном расположении валов соединяемых машин, торцевые плоскости полумуфт окажутся непараллельными и раскроются вверху. Оси не будут продолжением одна другой и валы в подобном устройстве во время эксплуатации начнут вибрировать. Образуются изгибающие моменты, вызывающие колоссальное напряжение на шейках валов. Для достижения параллельности плоскостей полумуфт, крайние подшипники валов располагают немного выше. Когда плоскости полумуфт станут параллельны, общая осевая линия двух валов станет плавной кривой. Чтобы монтировать роторы по такому принципу, нужно проверить линию валов соединяемых машин по уровню. Затем валы центрируются.
Выверка линии валов по уровню
Линия валов выверяется при совместной установке двух машин, таких как двигатель и генератор. Процедура производится тремя способами:
1.Вал первой машины устанавливается строго горизонтально. На каждой из шеек вала устанавливается уровень. У подшипников, монтированных с противоположных концов вала, показания уровней должны быть аналогичными по величине и обратными по знаку. Тогда прямая, пролегающая через центры концов вала, должна размещаться в горизонтальной плоскости. После этого, к валу первой машины прицентровывают вал второй. Установка уровня на шейку второго вала вблизи места стыковки должна дать такие же показания по величине и направлению, что и на шейке первого вала.
2. Конец вала машины у муфты располагают горизонтально, с нулевым отклонением по уровню у места стыковки. Противоположный конец вала немного приподнимают. Затем две машины прицентровываются друг к другу. При этом уровень на шейке подшипника другого вала у места стыковки должен показывать нулевое отклонение.
3. Вал первой машины располагается с небольшим подъёмом в одном направлении, то есть показания уровня на концах вала указывают уклон в одном направлении. Вал второй машины устанавливается так, чтобы уровень на шейке вала у места стыковки показывал отклонение с такой же величиной и уровнем.
При правильном монтаже линии валов по любому из трёх способов, торцы полумуфт должны располагаться параллельны. Измерения уклона шейки вала посредством уровня проводят в четырёх положениях вала, смещённых на 90°. В каждом положении выполняют два измерения, разворачивая уровень на 180° при втором. Действительная величина уклона вычисляется как среднее арифметическое восьми данных. При конусности шеек вала, уклон определяют с поправкой ае, которая вычисляется по формуле:
at = +- е/2 x k x l, где:
е – конусность шейки или разность диаметров на длине шейки вала, мм;
k – цена деления уровня, мм;
l – длина шейки вала, м.
Знак в начале формулы зависит от вектора конусности. Поправка ае прибавляется к расчёту уклона шейки вала с учётом конусности, когда направление конусности схоже с направлением подъёма вала. Вычитается поправка в случае, когда направление не соответствует. Данный метод позволяет избежать ошибок при искривлении ротора или отклонения оси шейки от оси вращения. На факт подобных дефектов указывает весомое изменение величин уровня на шейке вала при разных положениях ротора. На практике строгая параллельность плоскостей полумуфт сложно достижима. Из-за этого валы соединяются с некоторой допустимой их несоосностью.
Несоосность валов
Взаимное размещение валов с боковым или угловым смещением центрируемых осей сравнительно друг друга называется несоосностью. Несоосность бывает следующих видов:
- Параллельная;
- Угловая;
- Реальная.
При параллельной несоосности считается, что оси вращения установлены на равном расстоянии между собой по всей длине вращающихся деталей. При угловой оси вращения размещены под углом друг к другу. Реальная несоосность состоит из параллельной и угловой.
Размер допустимого смещения зависит от устройства используемых муфт. Разные типы муфт по-разному компенсируют неточность выверки соосности валов соединяемых машин. Муфты М3 имеют наибольшую компенсационную способность. Допустимое боковое смещение валов для данных муфт составляет от 0,7 до 4,8 мм, пределы бокового смещения для упругих втулочно-пальцевых муфт - от 0,3 до 0,6 мм. Для обоих типов допускается угловое смещение до 1, или в линейном представлении – 3,5 мм для муфт диаметром 400 мм; 4,3 мм для диаметра 500 мм и 5,2 мм для диаметра 600 мм. Применение жёсткой поперечно-свёртной муфты для соединения валов не допускает бокового и углового смещения. Данное соединение предполагает работу соединённых валов как одного общего. Тогда требуется более точная центровка валов. Угловые зазоры такого соединения на разных скоростях вращения не должны превосходить следующие показатели:
- от 0,04 до 0,05 мм при 3000 об/мин;
- от 0,08 до 0,11 мм при 1500 об/мин;
- от 0,1 до 0,12 мм при 750 об/мин;
- от 0,15 до 0,20 при 500 об/мин.
Устройства и приспособления для ликвидации несоосности
Несоосность устраняют:
- посредством линейки;
- с применением щупов;
- при эксплуатации радиально-осевых скоб;
- способом «обхода одной точкой»;
- часовыми индикаторами;
- лазерными системами;
- по полумуфтам.
с помощью линейки. Линейку прикладывают к муфте в вертикальной и горизонтальной плоскостях и определяют отклонение путём визуальной оценки зазора. Точность подобных измерений не превышает 1000 мкм.
с применением щупов измеряют соосность валов одинакового диаметра без полумуфт.
при использовании радиально-осевых скоб. При работе без необходимости осевого перемещения валов применяют одиночную пару скоб, для компенсации осевых смещений — две пары. Точность расчётов и центровки достигает 20-30 мкм. Для частот вращения вала 1500, 750, 500 об/мин допустимая разница диаметрально противоположных зазоров между центровочными скобами составляет 0,07–0,11; 0,1–0,12; 0,15–0,2 мм соответственно.
Скобы состоят из:
1, 10 – концы вала;
2, 8 – штативы;
3, 9 – хомуты;
4, 6 – кронштейны;
5, 7 – микрометрические винты.
К концу 1 вала хомутом 3 монтируется штатив 2 с кронштейном 4 и микрометрическим винтом 5. На конце 10 вала устанавливается штатив 8 с кронштейном и микрометрическим винтом 7. Микрометрические винты 5 и 7 измеряют радиальные и осевые зазоры соответственно.
метод «обхода одной точкой» проводится при невозможности обеспечить подвижность одной из частей системы. В работе используют щупы и обычные линейки. Точность центровки агрегата не превышает 500 мкм.
часовые индикаторы. Технология показана только для центровки валов по полумуфтам большого диаметра и предварительной проверки и диагностики несоосности. Снятие данных проводят по ободу и на фланце полумуфты, что помогает установить параллельную и угловую несоосность. Погрешность центровки привода составляет 1-10 мкм.
лазерными системами. Лазерные лучи измеряют взаимное перемещение вращающихся деталей и расчёт требуемых коррекций в следующем порядке:
1.Зафиксировать допустимую несоосность проверяемого оборудования по техпаспорту.
2. Проверить крепление опорных лап.
3. Разместить детекторы в необходимых точках проверяемых валов или полумуфт.
4. Выбрать нужную программу центровки.
5. Провернуть вал. При этом система сама идентифицирует положение датчиков и создаёт, визуализирует результат.
6. Исправить положение подвижного агрегата перемещением в вертикальной и горизонтальной плоскости. Если нужно, эксплуатировать калибровочные пластины.
7.Закрепить опорные лапы.
8. Провернуть вал. Удостовериться, что несоосность находится в границах допуска.
по полумуфтам. В скобу вкручивают измерительный болт с контргайкой. Боковые зазоры измеряют с применением щупа между измерительным болтом (или индикатором) и внешней поверхностью полумуфты, а угловые зазоры - между торцами полумуфт. В каждом положении полумуфт (0, 90, 180, 270) замеряют один боковой замер и два или четыре угловых зазора. Средние величины угловых зазоров при нескольких замерах определяют как среднее арифметическое путём деления суммы числовых значений зазоров на количество замеров.
Ниже представлены:
1 - скоба;
2 - болт;
3 – измерительный болт.
Купить подшипники можно в интернет-магазине “Промышленная Автоматизация”.
Оставить заявку или получить обратную связь вы можете написав нам на info@industriation.ru или позвонив по бесплатному номеру 8 800 550-72-52. Специалисты отдела продаж подберут оборудование, проконсультируют по возникшим вопросам и проконтролируют поставку.