Испытания подшипников
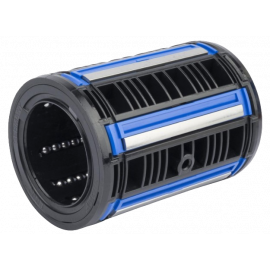
Что такое испытания подшипников?
Испытания подшипника – процесс проверки нагруженного подшипника и последующее сравнение полученных результатов с установленными пороговыми значениями. Благодаря испытаниям:
– оценивается эффективность использования новых конструкций, материалов, технологических процессов, методов смазки;
– расширяются сферы применения опоры;
– создаются высокотемпературные подшипники, для работы в неблагоприятных средах, в вакууме и т.д.
Виды испытаний подшипников
Испытания подшипника бывают трёх типов:
- ресурсные;
- контрольные;
- специальные;
Ресурсные испытания, т.е. испытания на фактический ресурс, определяют динамическую грузоподъёмность подшипника определённого типоразмера. Контрольные испытания оценивают качество деталей, изготавливаемых подшипниковыми заводами. Специальные испытания оценивают эффективность применения новых материалов, смазок, конструктивных или технологических мероприятий.
Методики испытания подшипников
Методика 1. Испытания выполняют при обороте внутреннего кольца. Для опор с оптимальными условиями работы скорость вращения составляет 0,4—0,6 от предельной для данного типа по каталогу и округляют по ряду: 500, 750, 1000, 1500, 2000, 2500, 3500, 4000, 5000, 7500 и 10 000 об/мин. Температура наружного кольца в процессе исследования не должна превышать 90°С.
Тестируемые опоры размещают на валу на тугой подшипниковой посадке, за исключением шариковых радиальных однорядных подшипников, которые монтируют на напряжённой подшипниковой посадке. Наружное кольцо закрепляют в корпус по скользящей подшипниковой посадке.
Работоспособность детали судят по таким показателям:
- гарантированный ресурс;
- контрольный ресурс.
Гарантированный ресурс — это наработка до предельного состояния, которую обеспечили 90% подшипников исследуемой партии. При определении ресурса учитываются только опоры, которые вышли из строя из-за усталостного разрушения. Контрольный ресурс — наработка до предельного состояния, которую обеспечили 90% тестируемых подшипников, несмотря на степень разрушения.
Методика 2 и её особенности:
1. Для всех опор указаны радиальные и осевые испытательные нагрузки, определяемые при определённых величинах контактных напряжений. Показатели определяются для любой конструктивной группы подшипников по кривым усталости, построенным после испытаний более 10 000 подшипников.
2. При исследовании группы подшипников применяют метод усечённых выборок. 20 опор тестируют до поломки восьми из них. Остальные 12 исследуют до наибольшего ресурса, выявленного при испытаниях восьми подшипников.
Испытания для оценки предельной частоты вращения подшипников
Предельная частота вращения подшипников трактуется параметром d,n'n^ где d,n—диаметр окружности, проходящей сквозь центры шариков или точку, находящуюся на оси ролика и делящую пополам его эффективную длину, мм; ^пр — предельная частота вращения, об/мин. Параметр зависит от конструкции, материалов подшипника, нагрузки, условий смазки, охлаждения. Под предельной частотой вращения, приведённой в каталогах, имеется в виду число оборотов в минуту, при котором опора проработает под нагрузкой несколько сотен часов. Несколько минут подшипник функционирует со значительно большей частотой (п — предельное кратковременное). Предельные ресурсные частоты вращения формируются по методике ВНИИПП (всероссийский научно-исследовательский институт подшипниковой промышленности): оценивается скорость по рабочей температуре и выходу из строя подшипников при возрастании скорости.
Исследуют 10 подшипников из одной партии. Опоры с классами точности 0 и 6 тестируют при увеличивающихся частотах вращения 0,75^пр, 1,25/Znp, 1,75ппр» 2^np (и, если возможно, при ещё большей частоте). Испытания на каждом режиме продолжаются ровно сутки, потом их прерывают для охлаждения подшипников до температуры окружающей среды. Нагрузка на опоры постоянна и выбирают при расчётном ресурсе 150—400 ч при максимальной ожидаемой частоте вращения. В рекомендуемом диапазоне ресурс выбирают с учётом интенсивности тепловыделения в подшипнике. Для шарикоподшипников с малым трением, при выборе нагрузки нацелены на ресурс в 150 ч; для конических подшипников придерживаются на максимальный ресурс.
Во время испытаний ежечасно отмечают температуру наружных колец подшипников. Температура повышается при переходе на высокие частоты вращения. Режим, при котором прирост температуры относительно окружающей среды превысит 50°С, считается предельным. Предельные частоты вращения в отдельных случаях ограничиваются работоспособностью сепаратора. Если на каком-либо режиме две или более опоры ломаются из-за разрушения сепаратора, то за предельный берут ближайший предшествующий режим.
Устройства для испытания подшипников
- В испытательных головках, сделанных по схеме ниже, испытуемые подшипники размещаются в отдельных корпусах 1, 2. На схеме ниже представлены:
1, 2 – корпус;
3 – коренной вал;
4 – шкив ременной передачи;
Fr – радиальная сила;
Fa – осевая сила.
Коренной вал 3 машины вращается от шкива 4 ременной передачи. Корпуса тестируемых подшипников подвижны в радиальном направлении относительно корпуса коренных подшипников. Нагружение радиальной силой Fr осуществляется с помощью рычажной или гидравлической системы. Возможно осевое нагружение испытываемых деталей, размещённых в корпусах 2. Расположение исследуемых подшипников в отдельных корпусах на консолях валов перекашивает кольца, особенно если корпуса не имеют надёжных направляющих.
- Другая схема испытательной головки представлена на схеме ниже. Здесь представлены:
1 – литой корпус;
2, 5 – гидростатические системы;
3 – испытываемый подшипник;
4 – коренной подшипник;
6 - муфта;
7 – приводной шкив;
8 – сменный шкив;
Fr – радиальная сила;
Fa – осевая сила.
В массивном жёстком литом корпусе 1 располагают сменную оснастку с четырьмя подшипниками: испытываемыми 3 и коренными 4. Гидростатические системы 2, 5 нагружают все четыре подшипника радиальными Fr силами и осевой Fa или комбинированной (Fr + Fa) силами два крайних подшипника 3. Привод машин содержит электродвигатель, клиноременную передачу со сменными шкивами 8 и муфту 6. Опоры приводного шкива 7 размещены в отдельном корпусе и разгружают исследуемые детали от сил натяжения ремня. Для увеличения частоты вращения между ременной передачей и коренным валом исследуемой головки размещается дополнительный зубчатый ускоритель.
- Испытательный стенд FE8 определяет свойства смазочных материалов, которые снижают износ подшипника. На стенде также проверяются технические масла и смазки. FE8 исследует:
– радиально-упорные шарикоподшипники;
– конические роликоподшипники;
– упорные цилиндрические роликоподшипники.
Упорный цилиндрический роликоподшипник применим лишь для испытаний масла. Остальные опоры эксплуатируются для тестирования технической смазки и масла.
В стенде FE8 используются осевые нагрузки от 5 кН до 100 кН. Диапазон скоростей - от 7,5 мин–1 до 4500 мин–1 (в специальной версии до 6000 мин–1). Некоторые рабочие циклы нагрузки/скорости не запускаются в тесте.
Данная методика исследований обеспечивает широкий диапазон режимов смазки от экстремального смешанного трения через умеренное смешанное трение до режима полностью несущего смазочную плёнку. С помощью осевого цилиндрического роликоподшипника образуется экстремальное смешанное трение и скольжение.
На схеме ниже:
Fa — аксиальная нагрузка;
1 — тестируемые подшипники;
2 — вспомогательный подшипник.
На стенде исследуется:
– защита от износа при экстремальном смешанном трении. Тестирование составлено на требованиях, аналогичных требованиям к трансмиссионным маслам «CLP» в соответствии с Din 51517. Разница лишь в том, что применяется высокая осевая нагрузка - 100 кН вместо 80 кН. Опоры испытываются в диапазоне экстремальных значений смешанного трения. Принимаются требования к износу тел качения, волнистость и остальные повреждения поверхности. Условия испытаний:
— скорость 7,5 мин–1;
— осевая нагрузка 100 кН;
— температура +80°C;
— время работы 80 часов.
– усталость при умеренном смешанном трении. Используются исследуемые подшипники «F-562831» с пластмассовым сепаратором. Сепаратор выделяется от ранее эксплуатирующегося свинченного пластикового сепаратора тем, что здесь на два кармана меньше, поэтому тестируемая нагрузка сокращена от 100 кН до 90 кН. После 800 часов тестирования не должно быть волнистости или точечной коррозии. Условия испытаний:
— скорость 75 мин–1;
— осевая нагрузка 90 Кн;
— температура +70 °C;
— наработка 800 часов.
– поведение технического масла. Здесь испытательный стенд FE8 применяется с контейнером предварительного нагрева. В данном испытании фигурируют некоторые аспекты:
— На редукторы влияет влага. Это происходит из-за условий окружающей среды или если внутри редуктора появляется конденсат.
— Образовавшаяся влага приводит к аддитивным реакциям. В совокупности с высокими температурами возникают отложения, что мешает фильтрации.
— Влага отрицательно влияет на смазочную плёнку, а осаждения присадок приводят к неблагоприятным реакционным слоям внутри подшипника.
Условия исследований:
— скорость 750 мин–1;
— осевая нагрузка 60 кН;
— температура +100°C на выходе из подогревателя;
— наработка 600 часов.
Подобный тест оценивается при получении наработки 600 часов без выхода подшипников из строя, образования нагара, загрязнения фильтра или износа тел качения.
- Испытательный стенд «FE9» определяет, возможно ли использовать смазку при высоких температурах опор качения. Во всех случаях радиально-упорный шарикоподшипник заполняется определённым объёмом смазки, подвергается осевой нагрузке и эксплуатируется с заданной скоростью. В зависимости от загустителя и базового масла, тестирование проводят при температурах от +100°C до +250°С. Проводят исследования на открытых опорах, с уплотнительными шайбами с двух сторон или с резервуаром для смазки. Обычным тестом, стандартизированным в «DIN 51821-2», является «A/1500/6000». В таком случае испытания проводят на открытой опоре осевой нагрузкой 1500 Н при частоте вращения 6000 мин–1.
На схеме ниже:
Fa — аксиальная нагрузка;
1 — изоляция;
2 — тестовый подшипник;
3 — вспомогательный подшипник;
4 — смазка входящая;
5 — смазка исходящая;
6 — нагревательный блок.
- Испытательный стенд А2 определяет защиту техническими маслами от износа, включая упорный цилиндрический роликоподшипник. Конструкция подобна испытательному стенду «FE8», основное отличие - тестирование осуществляется с использованием маслоотстойника. Поэтому необходимо немного технического масла. Исследование производится на скорости 11 мин–1 при осевой нагрузке 51,5 кН. Возможны температуры до +160°C.
- Испытательный стенд LFT оценивают защиту маслами против износа и образования смазочной плёнки. Исследуется упорный цилиндрический роликоподшипник с пластмассовым сепаратором, используется конструкция с вертикальным валом. Опора частично опускается с телами качения в масло. Определяется износ и контактное напряжение, которые применяются как индикатор формирования смазочной плёнки. Возможны скорости от 10 мин–1 до 4000 мин–1 при осевой нагрузке от 0,5 кН до 100 кН.
- Испытательный стенд АН42. Технические смазки размягчаются при использовании. Когда удары и высокочастотные вибрации влияют на техническую смазку продолжительное время, меняется состояние консистенции. Для этого и применяют стенд «AH42» с эксплуатацией метода «вибрационного сита». В тесте рабочий вал создаёт дисбаланс для формирования вибрации. Исследования производятся на скоростях от 1000 мин–1 до 2000 мин–1 при ускорении до 15g. Консистенцию смазки в испытуемом подшипнике определяют после 96 часов тестирования.
- Испытательная установка WS22. У технических смазок под высокие скорости особые требования к системам загустителей и базовым маслам. Смазки исследуются на специальных высокоскоростных испытательных стендах, например на WS22. Здесь два высокоточных подшипника шпинделя при небольшой осевой и радиальной нагрузке вращаются на скорости до 60000 мин–1. Значение соответствует параметру скорости 2000000 мин–1 · мм. Тестирование проводят с вращающимся внутренним кольцом, определяют температуру на неподвижном наружном кольце и наработку до разрушения.
На схеме ниже:
Fa — аксиальная нагрузка;
Fr — радиальная нагрузка.
- Испытательная установка WS10. При применении опоры с вращающимся наружным кольцом, особенно в подшипниковых узлах работающих на высоких скоростях, к технической смазке предъявляются дополнительные требования. Для определения соответствия требованиям создана испытательная установка «WS10».
Радиальная нагрузка создаётся натяжением ремня и силой веса, осевая передаётся с помощью тарельчатых пружин. Максимальная скорость наружного кольца составляет 4000 мин–1. Возможны скоростные параметры до 650000 мин–1·мм.
Купить подшипники можно в интернет-магазине “Промышленная Автоматизация”.
Оставить заявку или получить обратную связь вы можете написав нам на info@industriation.ru или позвонив по бесплатному номеру 8 800 550-72-52. Специалисты отдела продаж подберут оборудование, проконсультируют по возникшим вопросам и проконтролируют поставку.